Greg Rhinehart, program manager in the Chief Operating Officer’s office, figured out a way to 3-D print parts that are used in the respirator masks on the adult COVID unit. Photo by Donn Jones
Greg Rhinehart is a program manager in VUMC’s Office of the Chief Operating Officer by day and a 3-D printing hobbyist by night. He enjoys tabletop historical gaming, and prints buildings, towns and figurines for a more immersive experience. Before COVID-19, he never expected that his day job and night hobby would intertwine and save the Medical Center potentially thousands of dollars in the process.
He would have to measure the defective part and recreate the schematic – essentially re-engineer the part. It took him a couple of hours, but he had a prototype to put on the printer.
David Meyer is a senior program manager in the Department of Emergency Preparedness, preparing for and responding to internal and external emergency situations throughout the Medical Center. He had a problem – staff on the adult COVID-19 unit on the eighth floor of Medical Center East were quickly becoming heavy users of respirator masks as personal protective equipment, and a small plastic part inside them about the size of a thumbnail was wearing out.
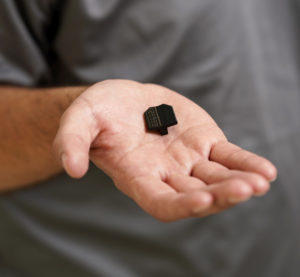
He called a representative of the manufacturer of the Powered Air Purifying Respirators (PAPR), who told him that the company doesn’t sell the part separately. Replacing a respirator would cost more than $1,500.
“They’re very expensive and they’re not really serviceable,” Rhinehart explained. “With a part that is broken on these units, it’s not something you can go to the manufacturer and say, hey I will take a dozen of these. Because the way the equipment is manufactured, it’s built in to a different piece.”
That gave Meyer an idea. He knew Rhinehart 3-D printed toy soldiers for fun. Could his printer, which he just purchased in December for his hobby, print the part Meyer needed?
Rhinehart, who worked as a machinist in college at Tennessee Tech University, thought he would give it a try. He had experience with rapid prototyping. He would have to measure the defective part and recreate the schematic – essentially re-engineer the part. It took him a couple of hours, but he had a prototype to put on the printer.
He printed a couple of the parts and gave them to Meyer. And the plan worked.
“Essentially, I was printing them and he was gluing them back together,” Rhinehart said.
The cost to make a part? “Three or four cents,” Rhinehart said.
“Every now and then you get to do a project that’s kind of extra rewarding.”
So Rhinehart is now printing the parts in batches of about a dozen, using a spool of plastic wire that resembles the kind used in a lawn trimmer. The process takes about 10 minutes.
“It takes longer for the machine to warm up and get ready than it does to print,” Rhinehart said.
Meyer said he has already replaced several this way.
Rhinehart said the newly-printed parts will have the same issue with wear, only now a replacement will be immediately available when needed.
It’s a gratifying addition to Rhinehart’s plate of work, which includes long-range planning, managing architectural drawings and data analysis.
“Every now and then you get to do a project that’s kind of extra rewarding — a little extra creativity, a little extra challenge, and this is one of those for me,” he said.